Pipeline Welding Inspection: Expert Providers for High-Quality Welds
Pipeline Welding Inspection: Expert Providers for High-Quality Welds
Blog Article
Understanding the Basics of Pipeline Welding Inspection: Essential Aspects for Reviewing Weld High Quality and Averting Failings
In the realm of pipeline welding evaluation, the stakes are without a doubt high, requiring a complete understanding of essential principles to make certain weld high quality and reduce failure risks. Different vital aspects come into play, consisting of the selection of ideal products, the application of sophisticated inspection strategies, and the recognition of widespread welding issues.
Value of Weld High Quality
The honesty of a pipe is fundamentally dependent on the top quality of its welds, making weld high quality a vital variable in ensuring secure and efficient procedure. A pipe weld offers as a junction point where materials are joined, and any type of shortages in this field can result in significant structural weak points. Poor weld top quality can cause leakages, ruptures, and tragic failings, positioning significant security risks and ecological dangers.
Several elements add to the high quality of a weld, consisting of the option of welding process, the skills of the welder, and the conditions under which the welding is done - Pipeline Welding Inspection. Poor prep work, improper warm input, and contamination can endanger weld integrity, causing issues such as porosity, incomplete combination, or cracks. As a result, stringent quality assurance steps must be executed throughout the welding process to minimize these risks
In addition, the long-lasting performance of a pipe is greatly affected by the sturdiness of its welds. Top quality welds not only improve the overall strength of the pipeline yet also prolong its service life, lowering the requirement for costly repairs and downtime. Therefore, making sure premium weld high quality is vital in pipe layout and upkeep techniques.
Trick Assessment Techniques
Ensuring weld high quality necessitates the implementation of reliable examination methods to identify possible problems prior to they cause failures. Pipeline Welding Inspection. Amongst the most extensively made use of techniques are aesthetic assessment, radiographic screening (RT), ultrasonic testing (UT), and magnetic fragment testing (MT) Each technique serves a distinctive objective and is chosen based upon the specific requirements of the pipe project
Aesthetic evaluation is the first line of defense, enabling assessors to evaluate surface area problems, positioning, and total handiwork. Radiographic testing provides a detailed sight of internal weld stability by making use of X-rays or gamma rays to find subsurface defects.
Ultrasonic testing utilizes high-frequency acoustic waves to review the density and integrity of welds, making it excellent for discovering interior gaps. Magnetic particle screening is a trustworthy technique for identifying surface and near-surface defects on ferromagnetic materials by using electromagnetic fields and great ferrous bits. By using these essential inspection strategies, pipeline welding inspectors can guarantee the finest requirements are maintained, ultimately bring about safer and a lot more trustworthy pipeline systems.
Common Welding Defects
In the world of pipeline welding, understanding usual welding flaws is important for maintaining structural integrity and security. These problems can lead to tragic failures otherwise recognized and dealt with promptly. Among one of the most prevalent defects are porosity, which takes place when gas allures in the weld metal, developing gaps that damage the joint. Another significant concern is absence of fusion, where the weld metal does not properly bond with the base material, jeopardizing the joint's toughness.

Fractures are also a vital concern, manifesting in numerous kinds such as warm cracks, cold cracks, and root cracks. Each type poses special obstacles and needs details examination techniques for detection. Undercut is another flaw that can minimize the weld's cross-sectional location, causing tension concentration points, while slag incorporation occurs when non-metallic material ends up being trapped in the weld pool, adversely impacting the mechanical homes of the weld.
Furthermore, inaccurate grain form can cause unequal anxiety circulation. Recognizing these common flaws is crucial for welders and inspectors alike, as very early discovery and adjustment are crucial to guaranteeing the long life and integrity of pipeline systems.

Products and Their Influence
Choosing the ideal materials for pipe welding significantly affects the total performance and dependability of the bonded joints. The choice of base steels, filler products, and coverings plays a crucial duty in establishing the toughness, deterioration resistance, and toughness of the welds. For circumstances, carbon steel is generally made use of for its balance of toughness and price, but it might be prone to corrosion in particular atmospheres, requiring the use of corrosion-resistant alloys or protective coverings.
Additionally, dissimilar metal welding needs cautious factor to consider of thermal development residential or commercial properties and possible galvanic rust. look at this site The compatibility of materials can considerably affect the microstructure of the weld, bring about variants in mechanical properties. For instance, stainless-steel uses excellent rust resistance yet might require why not try this out certain filler products to guarantee a sound weld joint.
Furthermore, the influence of temperature level and ecological problems on product choice can not be taken too lightly. High-strength steels may shed ductility at elevated temperature levels, while low-temperature applications may call for products with enhanced durability. Inevitably, understanding the effects of material selections is important for accomplishing optimal weld quality and avoiding failings in pipeline systems.
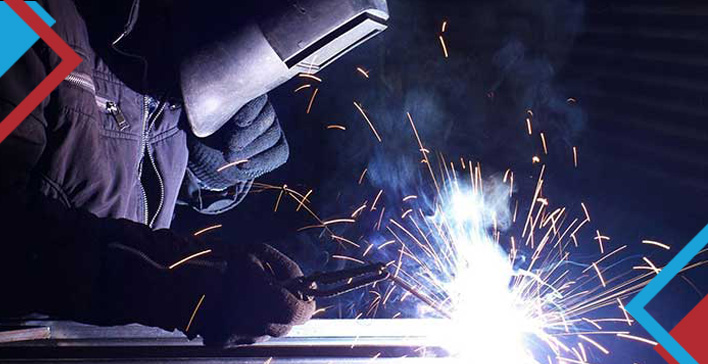
Regulative Criteria and Conformity
Regulative criteria and conformity play a pivotal duty in pipeline welding, developing the structure within which efficient and safe techniques are kept. These requirements are developed by numerous organizations, including the American Society of Mechanical Engineers (ASME), the American Welding Culture (AWS), and the Pipe and Hazardous Products Safety Administration (PHMSA) Complying with these guidelines ensures that welding treatments meet the required top quality and safety standards.
Conformity with governing requirements is essential not just for ensuring the honesty of the welds but likewise for shielding the setting and public security. Inspectors are tasked with validating that welding procedures abide with these requirements via strenuous evaluations of both the procedures and the last welds. This entails evaluating welder certifications, welding procedures, and the products utilized.
Failure to abide by established regulations can bring about considerable effects, including expensive repair work, legal liabilities, and devastating failings. For that reason, organizations have to incorporate compliance into their operational methods, fostering a culture of security and quality. Normal training and audits are essential parts in maintaining adherence to these governing criteria, making certain that all workers are knowledgeable and geared up to support the highest degree of pipeline welding quality.
Final Thought
In verdict, an extensive understanding of pipeline welding examination is essential for making sure weld high quality and protecting against failings. By utilizing vital assessment methods and identifying usual welding issues, examiners can successfully analyze the stability of welds.
In the world of pipe welding assessment, the stakes are without a doubt high, requiring a complete understanding of essential concepts to make certain weld quality and mitigate failing dangers (Pipeline Welding Inspection).The honesty of a pipeline is fundamentally dependent on the top quality of its welds, making weld top quality a vital factor in making certain efficient browse around here and secure operation.Several elements add to the high quality of a weld, consisting of the choice of welding procedure, the abilities of the welder, and the conditions under which the welding is executed. Undercut is an additional issue that can decrease the weld's cross-sectional area, leading to stress and anxiety focus factors, while slag incorporation takes place when non-metallic material becomes caught in the weld pool, detrimentally influencing the mechanical buildings of the weld
In verdict, a detailed understanding of pipeline welding evaluation is crucial for ensuring weld top quality and preventing failures.
Report this page